Take Note
Donate for mothers
UAB has a critical need for blood products. Donate 9 a.m.-3 p.m. May 13-16 and get a $20 e-gift card to a merchant of your choice, a t-shirt and a $20 Amazon e-gift card. Make an appointment online.
Register for UAB 2025 summer camps ☀️
Fun and educational summer camps include opportunities to learn more about visual arts, science, creative writing, cooking, business careers and more. See a list of camps, dates and contact information online.
5th Annual Student Success Summit
This event, 9 a.m.-4 p.m. May 14, is for faculty and staff to discuss student success at UAB, with progress reports on the Student SUCCESS Initiative an table discussions; register online.

People of UAB May 13, 2025
Next-Gen IT gives students, and employees, a career boost
Two young alumni employees in UAB IT have turned a student’s idea into a department-wide development opportunity. Next-Gen IT has helped multiple IT student assistants land full-time jobs with the university and given employees a chance to hone their networking and soft skills, too.
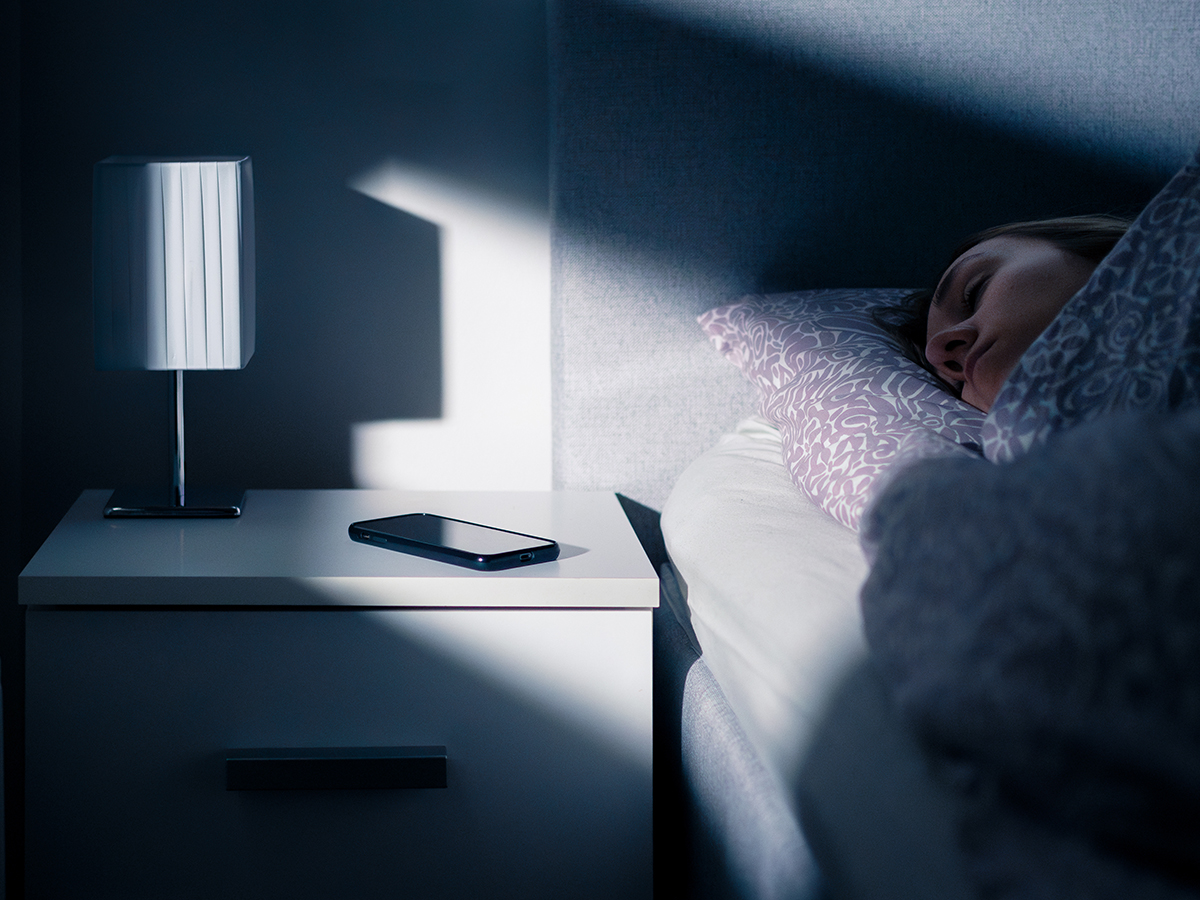
Research & Innovation April 30, 2025
Better sleep without drugs: How cognitive behavioral therapy for insomnia works
Experience more on social
Share your Blazer pride in the UAB people and places you love on our social media channels. Be sure to follow us so you don't miss the stories, photos, and video we produce just for our social media audiences.

myUAB Portal
Access customizable tools and resources
The myUAB portal is your UAB home page for work or school. Select your frequently used features, see official notifications, and keep up with news and events.
Go to myUAB PortaleReporter
Browse Past Editions of the eReporter
If you missed or want to revisit one of Tuesday or Friday email newsletters, you can find it in our Digital Commons archive.
Browse Past EditionsSubscription Center
Manage your email newsletters
The eReporter is automatically delivered to UAB employees twice each week. To sign up for additional UAB email newsletters, browse our Subscription Center.
Manage Subscriptions